Pump Room Solutions
API 610 Cargo Pump Arrangement with Eureka BB2
Eureka’s API 610 Cargo Pump Systems are engineered for high-efficiency cargo transfer in FPSOs, chemical plants, and industrial applications. Based on the robust BB2 pump design, the system offers long service intervals, reliable operation, and full compliance with API 610 and API 682 standards. With multiple configuration options, pressurized barrier-fluid sealing systems, and integrated control solutions, this cargo handling package delivers safe, efficient, and fully optimized pump room performance.
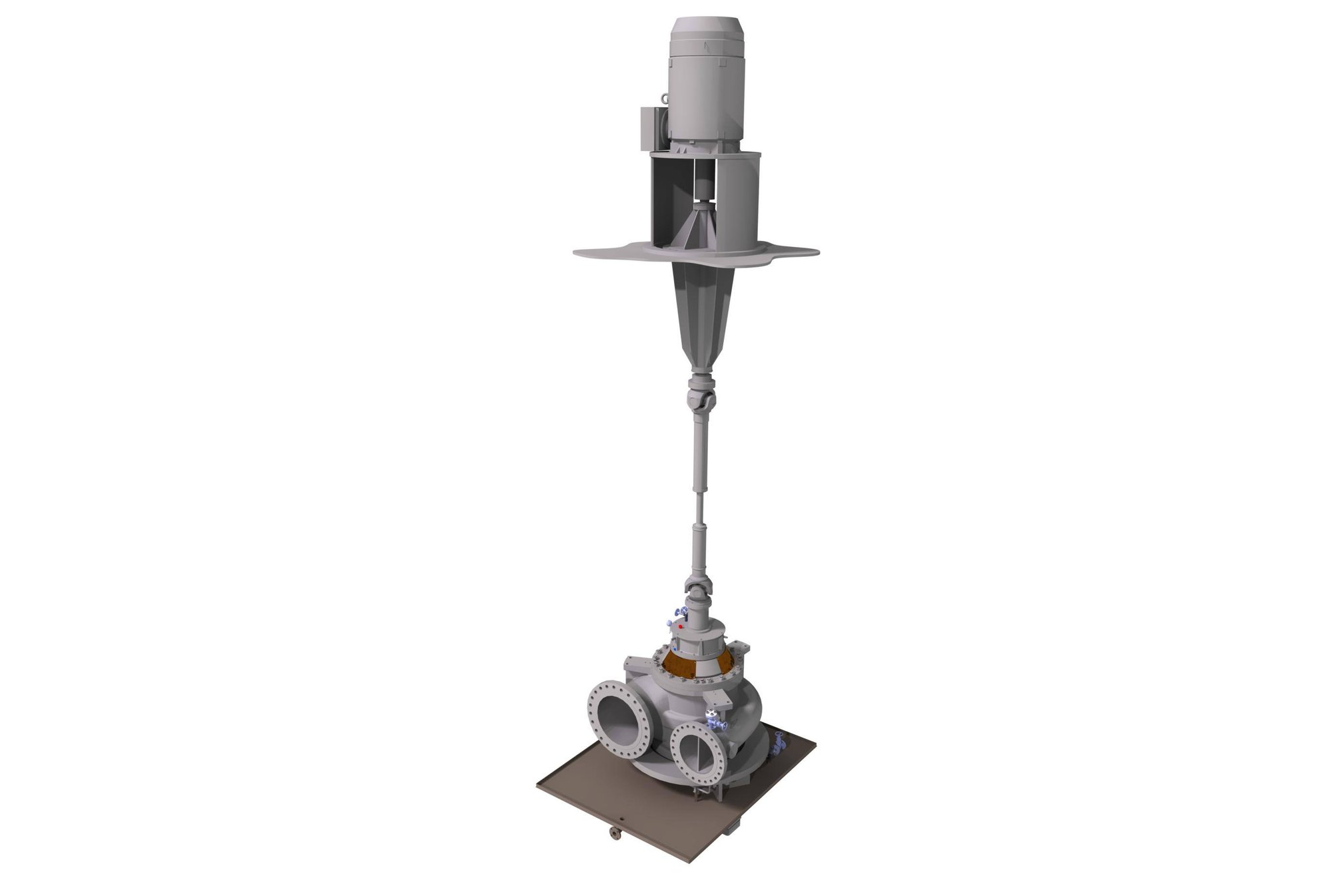
Main Features & Benefits
- Single pump design meets discharge pressure requirements on its own
- API 610-compliant for high-pressure cargo transfer
- Wide material selection in accordance with API 610
- Supports high nozzle loads for structural integrity
- Low NPSH operation prevents cavitation and increases pump life
- Variable speed operation via hydraulic coupling or frequency converter
- Fully integrated system with cargo, stripping, ballast, and tank-washing pumps and drivers
- Eureka control system for full monitoring and control
- Pressurized API 682 double mechanical seal prevents hydrocarbon leakage
- Safe FPSO offloading with speed control to match tank level and NPSH
Description
The system consists of one or more API 610 BB2 centrifugal pumps driven by fixed or variable speed motors, typically arranged in horizontal or vertical configurations, depending on the layout. The motor and pump can be installed in separate compartments, requiring a gas-tight transmission or coupling. Each system is engineered to deliver optimized flow, pressure, and control during cargo transfer operations.
Key Design Features:
- Pump type: Single-stage, double-suction, double volute, radially split BB2 design
- Drive options: Fixed speed, hydraulic coupling, or VFD (variable frequency drive)
- Mechanical seal: API 682 double mechanical seal system with pressurized barrier fluid (Plan 53B)
- NPSH control: Pump speed reduces as tank empties to avoid cavitation
- Possible configuration: 3 × 50% or 4 × 33% pumps, one standby always available
- Optional: Priming system on suction side
Read more about the Eureka BB2 Pump
Pump Casing & Cover
- Radially split casing with double volute for reduced radial loads
- Integrated mounting ribs for efficient nozzle load transfer
- Inline, side-side, or top-top nozzle configurations available (horizontal or vertical execution)
Seal Chamber & Mechanical Seal
- One deep API 682-compliant chamber (No non-drive end penetration)
- Double mechanical seal with pressurized external barrier system (Plan 53B)
- Internal pumping ring and higher-than-discharge pressure ensures sealing integrity
Shaft & Bearings
- Heavy-duty shaft with minimal deflection for improved reliability
- Process-lubricated silicon carbide journal bearings (non-drive end)
- Oil-lubricated anti-friction or tilting pad thrust bearing (drive end)
Impeller Wear Rings
- Double-suction impeller for balanced axial loads and low NPSH
- Shrink-fit and mechanically secured impeller wear rings
- Wear rings installed with interference fit and mechanically secured
Throat Bushing & Shaft Sleeve
- Throat bushing for controlling seal flush flow rate
- Keyed shaft sleeves, axially positioning the impeller, fixed by shaft lock nut
Gaskets & Coupling
- O-ring sealing between casing parts
- Spacer-type flexible coupling allows seal and bearing service without motor removal